AI Optimizes Production Through Capacity Constraint Job Scheduling
In today's competitive manufacturing world, fine-tuning production processes is essential for cutting costs and boosting efficiency. One major hurdle is capacity constraint job scheduling, which involves juggling limited resources and intricate dependencies to meet customer needs. Innotock AI steps in with a robust solution, using sophisticated algorithms to nail down the best production sequence. This approach not only slashes total costs but also smartly handles shared capacity limits across machines and ensures timely delivery to customers. This piece delves into how Innotock AI tackles this tricky challenge, giving businesses a leg up in supply chain optimization.
Key Points
- Capacity Constraint Job Scheduling: Tackles the challenge of optimizing production under tight resource constraints.
- Innotock AI Solution: Uses cutting-edge AI algorithms to find the ideal production sequence.
- Cost Minimization: Aims to reduce total costs, including direct production, setup, inventory, and late delivery fees.
- Efficient Resource Management: Manages shared capacity constraints across multiple machines.
- Customer Demand: Focuses on meeting customer needs promptly and efficiently.
- Optimal Production Sequence: Determines the best order for producing items to cut costs and enhance efficiency.
- Python and PuLP: Employs Python and PuLP linear programming for modeling and optimization.
- Sensitivity Analysis: Compares different production strategies to find the most resilient solutions.
- Gross Margin Improvement: Boosts gross margins by lowering costs and increasing productivity.
- Supply Chain Optimization: Offers a smart system for overall supply chain efficiency.
Understanding Capacity Constraint Job Scheduling
What is Capacity Constraint Job Scheduling?
Capacity constraint job scheduling is a complex puzzle that involves figuring out the most efficient way to sequence production jobs while taking into account limited resources. These resources—or constraints—can range from machine capacity to labor and material availability, all of which can bottleneck the production process. The aim is to craft a schedule that minimizes costs, meets customer demand, and maximizes resource use. This is a key part of supply chain optimization because it directly affects how efficiently and profitably a business can produce.
Effective job scheduling requires a deep dive into various factors like production costs, setup times, inventory costs, and potential penalties for late deliveries. Traditional methods and planning tools often struggle with these complexities, leading to less-than-ideal schedules and higher costs. This is where Innotock AI shines, offering the power to sift through massive amounts of data and produce optimized schedules that streamline operations.
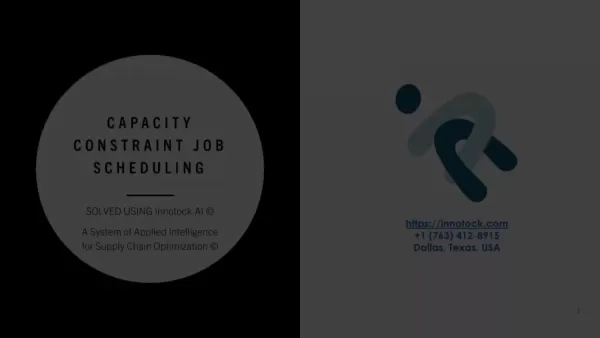
The key elements of capacity constraint job scheduling include:
- Demand Forecasting: Accurately predicting customer demand to plan production effectively.
- Resource Allocation: Efficiently distributing available resources across different production jobs.
- Sequencing: Deciding the best order to carry out production jobs.
- Constraint Management: Dealing with limitations like machine capacity, labor, and material availability.
- Cost Optimization: Cutting down total costs linked to production, setup, inventory, and late deliveries.
By tackling these elements head-on, businesses can develop production schedules that are not only cost-effective but also nimble enough to respond to customer needs. Capacity constraint job scheduling is thus a vital piece of the modern supply chain puzzle.
The Challenge of Finding the Optimal Production Sequence
Finding the best production sequence is a multifaceted challenge that involves juggling various cost factors. The goal is to minimize total costs while ensuring customer demand is met, which means balancing direct production costs, setup costs, inventory carrying costs, and penalties for late deliveries. Each of these factors plays a part in the overall cost of production, and the right sequence can make a big dent in these expenses.
Direct production costs include materials, labor, and overhead. Setup costs come into play when switching between different production jobs, requiring machines to be reconfigured. Inventory carrying costs account for the expense of storing and managing inventory. And then there are customer chargebacks for late delivery, which are penalties for missing deadlines.
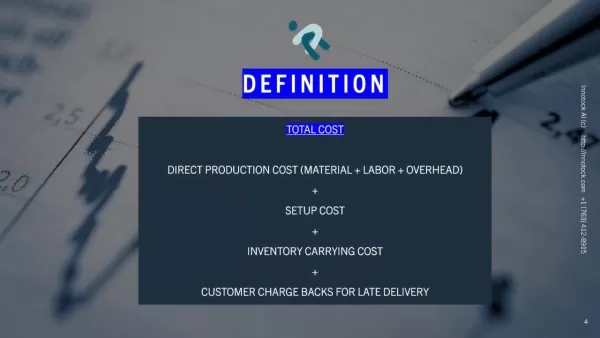
Total cost is the sum of these individual cost components:
- Direct Production Cost: Materials + Labor + Overhead
- Setup Cost: Costs for changing machine configurations.
- Inventory Carrying Cost: Expenses for storing and managing inventory.
- Customer Chargebacks for Late Delivery: Penalties for missing delivery deadlines.
The trickiness of finding the optimal production sequence stems from the interdependencies among these cost factors. For instance, cutting setup costs might boost inventory carrying costs, or minimizing direct production costs might lead to late deliveries. That's why a holistic approach is needed to balance these competing goals and pinpoint the sequence that yields the lowest total cost. Advanced AI solutions like Innotock AI are invaluable here, as they can untangle these complex relationships and uncover optimal solutions that traditional methods might miss. By accurately modeling these cost components and their interactions, businesses can make smarter decisions about production sequencing and significantly improve their bottom line.
Innotock AI: A Solution for Optimal Production Scheduling
How Innotock AI Solves Capacity Constraint Job Scheduling
Innotock AI provides a comprehensive solution to the capacity constraint job scheduling problem by harnessing advanced AI and optimization algorithms. The system is engineered to pinpoint the optimal production sequence that minimizes total costs while considering all relevant constraints and objectives.
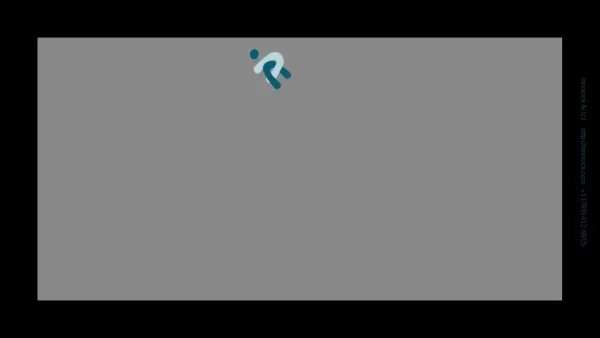
Key methods and tools used by Innotock AI include:
- Innotock Optimization Algorithms: Custom algorithms designed for efficient and accurate optimization of production schedules.
- Python: A versatile programming language used for modeling and implementing the optimization algorithms.
- PuLP Linear Programming: A linear programming solver used to find optimal solutions to the scheduling problem.
- Matplotlib Chart: A library to visualize and analyze the results of the optimization process.
By leveraging these tools, Innotock AI can efficiently process large datasets, model complex relationships, and generate optimized production schedules. The system handles various constraints, including machine capacity, labor availability, material supply, and customer delivery deadlines, while also considering different cost factors like direct production costs, setup costs, inventory carrying costs, and late delivery charges.
The process involves feeding in relevant data, such as demand by product by period, product routing machine setup times, and other operational and financial data. The system then applies the optimization algorithms to produce a production schedule that minimizes total costs while meeting customer demand and adhering to all constraints. This approach offers a significant leap over manual methods and traditional planning tools, which often struggle to grasp the problem's complexity.
Innotock AI's solution also features a sensitivity analysis tool, allowing businesses to compare different production strategies and gauge their resilience under varying conditions. This provides valuable insights for making informed decisions and adapting to shifting market dynamics. The result is a more efficient, cost-effective, and responsive production process, leading to enhanced profitability and customer satisfaction.
Input Data and Constraints
To effectively optimize production scheduling, Innotock AI requires a variety of input data and consideration of several constraints. Accurate and comprehensive data is crucial for generating realistic and actionable schedules.
Key input data includes:
- Demand by Product by Period: This data includes the quantity of each product required for each time period. Accurate demand forecasting is essential for effective production planning.
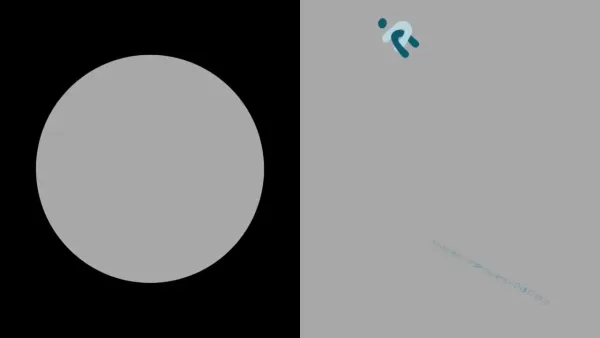
- Product Routing Machine Setup Times: This data defines the sequence of machines required to produce each product, along with the setup times for changing between products on each machine.
- Other Operational/Financial Data: This includes various input variables such as the number of working days per week, number of shifts per day, overall equipment effectiveness (OEE), cost per machine hour, cost per labor hour, setup costs, and markup percentage.
Key constraints include:
- A Machine Can Only Manufacture One Product at a Time: This ensures that machines are not overloaded and that production is feasible.
- There Are Routings That Must Be Followed: This ensures that products are produced in the correct sequence of machines.
- The Due Date for Every Job is the Last Day of the Demand Period for That Job: This ensures that production meets customer delivery deadlines.
- Minimize WIP and Finished Good Inventory: This objective aims to reduce inventory carrying costs and improve cash flow.
- Minimize Chargebacks from Customers: This objective aims to reduce penalties for late deliveries.
By incorporating these input data and constraints, Innotock AI can generate production schedules that are both feasible and cost-effective. The system is designed to handle a wide range of real-world scenarios, providing businesses with the flexibility and adaptability needed to thrive in today's dynamic market.
Comparing Production Strategies: Manual vs. Optimized
To illustrate the effectiveness of Innotock AI, it's helpful to compare different production strategies. The two main approaches are the manual strategy ("Compact") and the AI-optimized strategy ("Optimal Sequence"). Understanding the differences between these approaches underscores the value of using AI for production scheduling.
Manual Strategy ("Compact")
The manual strategy, often dubbed "Compact," typically involves scheduling production jobs based on experience, intuition, and simple rules. This approach may aim to minimize setup times or maximize machine utilization, but it often overlooks the complex interplay among different cost factors and constraints. As a result, the manual strategy can lead to suboptimal schedules with higher total costs and lower gross margins.
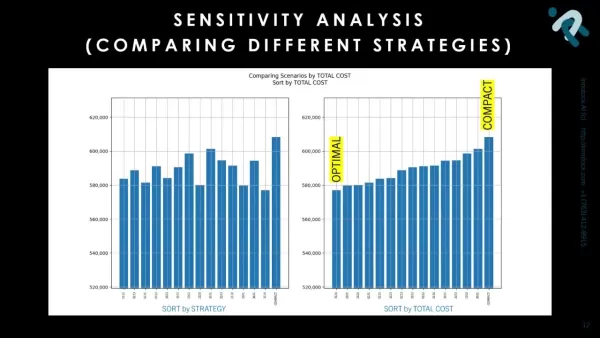
AI-Optimized Strategy ("Optimal Sequence")
The AI-optimized strategy, powered by Innotock AI, leverages advanced algorithms to generate the optimal production sequence. This approach takes into account all relevant cost factors, constraints, and objectives to create a schedule that minimizes total costs while meeting customer demand. The AI-optimized strategy can spot opportunities for cost savings and efficiency gains that manual methods might miss.
Comparison of Results
Metric Compact Opt Plan % Improvement Makespan (Hours) 677.89 590.75 -12.85 Total Revenue ($) 765,245.99 765,245.99 0.00 Direct Cost ($) 510,163.99 510,163.99 0.00 Total Setup Cost ($) 49,560.00 49,560.00 0.00 Inventory Penalty ($) 1,203.00 3,251.00 170.24 Expected C/Backs ($) 47,212.00 13,873.00 -70.62 Total Cost ($) 608,138.99 576,847.99 -5.15 Gross Margin ($) 206,654.00 237,945.00 15.14 Gross Margin (%) 27.53 31.04 12.75
The optimized sequence cuts completion time by 12.85% and reduces costs by 5.15%, yielding a Gross Margin of 31.04% versus 27.53% compared to the manual approach.
Related article
Elevate Your Images with HitPaw AI Photo Enhancer: A Comprehensive Guide
Want to transform your photo editing experience? Thanks to cutting-edge artificial intelligence, improving your images is now effortless. This detailed guide explores the HitPaw AI Photo Enhancer, an
AI-Powered Music Creation: Craft Songs and Videos Effortlessly
Music creation can be complex, demanding time, resources, and expertise. Artificial intelligence has transformed this process, making it simple and accessible. This guide highlights how AI enables any
Creating AI-Powered Coloring Books: A Comprehensive Guide
Designing coloring books is a rewarding pursuit, combining artistic expression with calming experiences for users. Yet, the process can be labor-intensive. Thankfully, AI tools simplify the creation o
Comments (1)
0/200
RogerLopez
July 28, 2025 at 2:45:48 AM EDT
This AI scheduling stuff sounds like a game-changer for factories! 🤖 Curious how it handles super complex production lines though.
0
In today's competitive manufacturing world, fine-tuning production processes is essential for cutting costs and boosting efficiency. One major hurdle is capacity constraint job scheduling, which involves juggling limited resources and intricate dependencies to meet customer needs. Innotock AI steps in with a robust solution, using sophisticated algorithms to nail down the best production sequence. This approach not only slashes total costs but also smartly handles shared capacity limits across machines and ensures timely delivery to customers. This piece delves into how Innotock AI tackles this tricky challenge, giving businesses a leg up in supply chain optimization.
Key Points
- Capacity Constraint Job Scheduling: Tackles the challenge of optimizing production under tight resource constraints.
- Innotock AI Solution: Uses cutting-edge AI algorithms to find the ideal production sequence.
- Cost Minimization: Aims to reduce total costs, including direct production, setup, inventory, and late delivery fees.
- Efficient Resource Management: Manages shared capacity constraints across multiple machines.
- Customer Demand: Focuses on meeting customer needs promptly and efficiently.
- Optimal Production Sequence: Determines the best order for producing items to cut costs and enhance efficiency.
- Python and PuLP: Employs Python and PuLP linear programming for modeling and optimization.
- Sensitivity Analysis: Compares different production strategies to find the most resilient solutions.
- Gross Margin Improvement: Boosts gross margins by lowering costs and increasing productivity.
- Supply Chain Optimization: Offers a smart system for overall supply chain efficiency.
Understanding Capacity Constraint Job Scheduling
What is Capacity Constraint Job Scheduling?
Capacity constraint job scheduling is a complex puzzle that involves figuring out the most efficient way to sequence production jobs while taking into account limited resources. These resources—or constraints—can range from machine capacity to labor and material availability, all of which can bottleneck the production process. The aim is to craft a schedule that minimizes costs, meets customer demand, and maximizes resource use. This is a key part of supply chain optimization because it directly affects how efficiently and profitably a business can produce.
Effective job scheduling requires a deep dive into various factors like production costs, setup times, inventory costs, and potential penalties for late deliveries. Traditional methods and planning tools often struggle with these complexities, leading to less-than-ideal schedules and higher costs. This is where Innotock AI shines, offering the power to sift through massive amounts of data and produce optimized schedules that streamline operations.
The key elements of capacity constraint job scheduling include:
- Demand Forecasting: Accurately predicting customer demand to plan production effectively.
- Resource Allocation: Efficiently distributing available resources across different production jobs.
- Sequencing: Deciding the best order to carry out production jobs.
- Constraint Management: Dealing with limitations like machine capacity, labor, and material availability.
- Cost Optimization: Cutting down total costs linked to production, setup, inventory, and late deliveries.
By tackling these elements head-on, businesses can develop production schedules that are not only cost-effective but also nimble enough to respond to customer needs. Capacity constraint job scheduling is thus a vital piece of the modern supply chain puzzle.
The Challenge of Finding the Optimal Production Sequence
Finding the best production sequence is a multifaceted challenge that involves juggling various cost factors. The goal is to minimize total costs while ensuring customer demand is met, which means balancing direct production costs, setup costs, inventory carrying costs, and penalties for late deliveries. Each of these factors plays a part in the overall cost of production, and the right sequence can make a big dent in these expenses.
Direct production costs include materials, labor, and overhead. Setup costs come into play when switching between different production jobs, requiring machines to be reconfigured. Inventory carrying costs account for the expense of storing and managing inventory. And then there are customer chargebacks for late delivery, which are penalties for missing deadlines.
Total cost is the sum of these individual cost components:
- Direct Production Cost: Materials + Labor + Overhead
- Setup Cost: Costs for changing machine configurations.
- Inventory Carrying Cost: Expenses for storing and managing inventory.
- Customer Chargebacks for Late Delivery: Penalties for missing delivery deadlines.
The trickiness of finding the optimal production sequence stems from the interdependencies among these cost factors. For instance, cutting setup costs might boost inventory carrying costs, or minimizing direct production costs might lead to late deliveries. That's why a holistic approach is needed to balance these competing goals and pinpoint the sequence that yields the lowest total cost. Advanced AI solutions like Innotock AI are invaluable here, as they can untangle these complex relationships and uncover optimal solutions that traditional methods might miss. By accurately modeling these cost components and their interactions, businesses can make smarter decisions about production sequencing and significantly improve their bottom line.
Innotock AI: A Solution for Optimal Production Scheduling
How Innotock AI Solves Capacity Constraint Job Scheduling
Innotock AI provides a comprehensive solution to the capacity constraint job scheduling problem by harnessing advanced AI and optimization algorithms. The system is engineered to pinpoint the optimal production sequence that minimizes total costs while considering all relevant constraints and objectives.
Key methods and tools used by Innotock AI include:
- Innotock Optimization Algorithms: Custom algorithms designed for efficient and accurate optimization of production schedules.
- Python: A versatile programming language used for modeling and implementing the optimization algorithms.
- PuLP Linear Programming: A linear programming solver used to find optimal solutions to the scheduling problem.
- Matplotlib Chart: A library to visualize and analyze the results of the optimization process.
By leveraging these tools, Innotock AI can efficiently process large datasets, model complex relationships, and generate optimized production schedules. The system handles various constraints, including machine capacity, labor availability, material supply, and customer delivery deadlines, while also considering different cost factors like direct production costs, setup costs, inventory carrying costs, and late delivery charges.
The process involves feeding in relevant data, such as demand by product by period, product routing machine setup times, and other operational and financial data. The system then applies the optimization algorithms to produce a production schedule that minimizes total costs while meeting customer demand and adhering to all constraints. This approach offers a significant leap over manual methods and traditional planning tools, which often struggle to grasp the problem's complexity.
Innotock AI's solution also features a sensitivity analysis tool, allowing businesses to compare different production strategies and gauge their resilience under varying conditions. This provides valuable insights for making informed decisions and adapting to shifting market dynamics. The result is a more efficient, cost-effective, and responsive production process, leading to enhanced profitability and customer satisfaction.
Input Data and Constraints
To effectively optimize production scheduling, Innotock AI requires a variety of input data and consideration of several constraints. Accurate and comprehensive data is crucial for generating realistic and actionable schedules.
Key input data includes:
- Demand by Product by Period: This data includes the quantity of each product required for each time period. Accurate demand forecasting is essential for effective production planning.
- Product Routing Machine Setup Times: This data defines the sequence of machines required to produce each product, along with the setup times for changing between products on each machine.
- Other Operational/Financial Data: This includes various input variables such as the number of working days per week, number of shifts per day, overall equipment effectiveness (OEE), cost per machine hour, cost per labor hour, setup costs, and markup percentage.
Key constraints include:
- A Machine Can Only Manufacture One Product at a Time: This ensures that machines are not overloaded and that production is feasible.
- There Are Routings That Must Be Followed: This ensures that products are produced in the correct sequence of machines.
- The Due Date for Every Job is the Last Day of the Demand Period for That Job: This ensures that production meets customer delivery deadlines.
- Minimize WIP and Finished Good Inventory: This objective aims to reduce inventory carrying costs and improve cash flow.
- Minimize Chargebacks from Customers: This objective aims to reduce penalties for late deliveries.
By incorporating these input data and constraints, Innotock AI can generate production schedules that are both feasible and cost-effective. The system is designed to handle a wide range of real-world scenarios, providing businesses with the flexibility and adaptability needed to thrive in today's dynamic market.
Comparing Production Strategies: Manual vs. Optimized
To illustrate the effectiveness of Innotock AI, it's helpful to compare different production strategies. The two main approaches are the manual strategy ("Compact") and the AI-optimized strategy ("Optimal Sequence"). Understanding the differences between these approaches underscores the value of using AI for production scheduling.
Manual Strategy ("Compact")
The manual strategy, often dubbed "Compact," typically involves scheduling production jobs based on experience, intuition, and simple rules. This approach may aim to minimize setup times or maximize machine utilization, but it often overlooks the complex interplay among different cost factors and constraints. As a result, the manual strategy can lead to suboptimal schedules with higher total costs and lower gross margins.
AI-Optimized Strategy ("Optimal Sequence")
The AI-optimized strategy, powered by Innotock AI, leverages advanced algorithms to generate the optimal production sequence. This approach takes into account all relevant cost factors, constraints, and objectives to create a schedule that minimizes total costs while meeting customer demand. The AI-optimized strategy can spot opportunities for cost savings and efficiency gains that manual methods might miss.
Comparison of Results
Metric | Compact | Opt Plan | % Improvement |
---|---|---|---|
Makespan (Hours) | 677.89 | 590.75 | -12.85 |
Total Revenue ($) | 765,245.99 | 765,245.99 | 0.00 |
Direct Cost ($) | 510,163.99 | 510,163.99 | 0.00 |
Total Setup Cost ($) | 49,560.00 | 49,560.00 | 0.00 |
Inventory Penalty ($) | 1,203.00 | 3,251.00 | 170.24 |
Expected C/Backs ($) | 47,212.00 | 13,873.00 | -70.62 |
Total Cost ($) | 608,138.99 | 576,847.99 | -5.15 |
Gross Margin ($) | 206,654.00 | 237,945.00 | 15.14 |
Gross Margin (%) | 27.53 | 31.04 | 12.75 |
The optimized sequence cuts completion time by 12.85% and reduces costs by 5.15%, yielding a Gross Margin of 31.04% versus 27.53% compared to the manual approach.
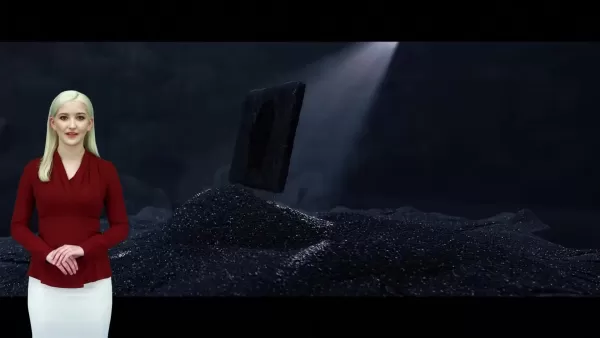
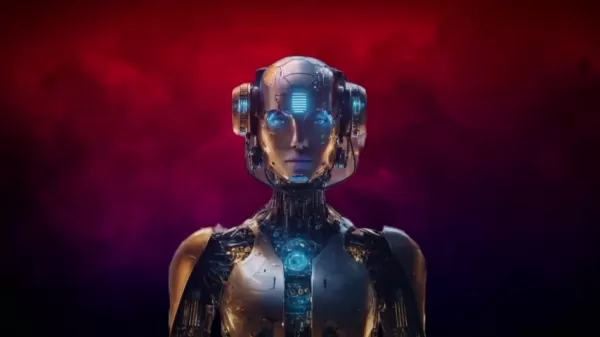
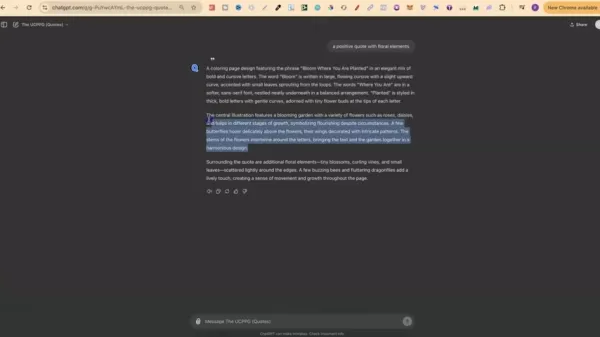

This AI scheduling stuff sounds like a game-changer for factories! 🤖 Curious how it handles super complex production lines though.



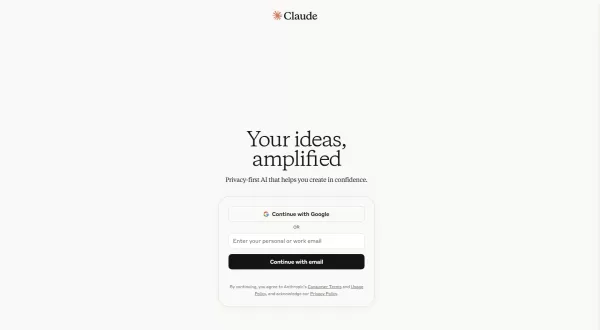
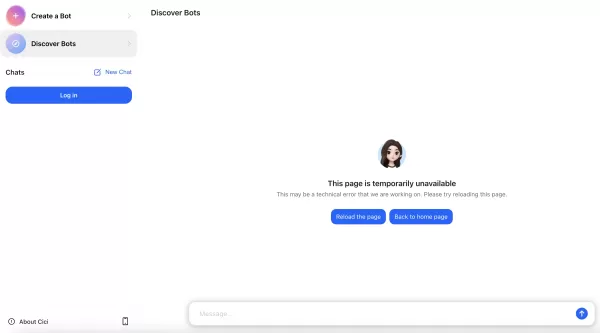
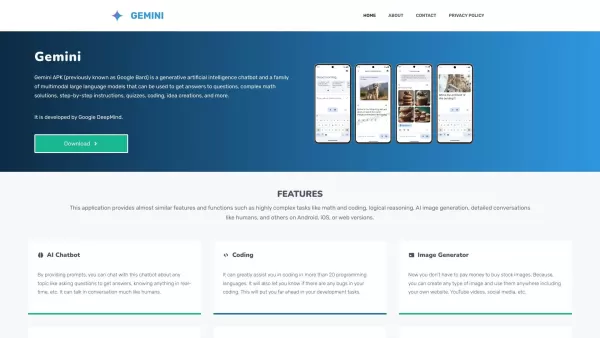
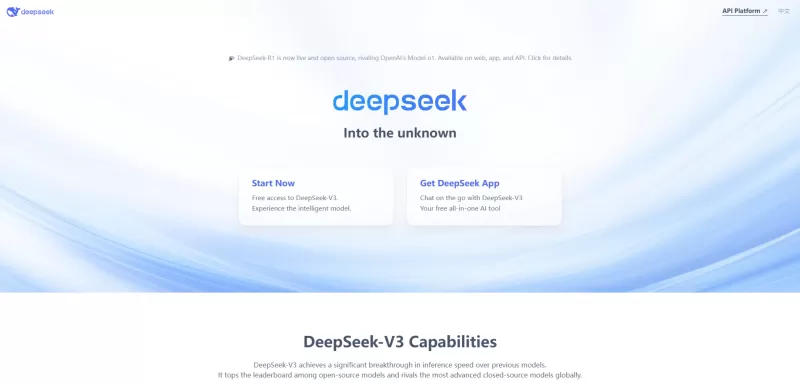
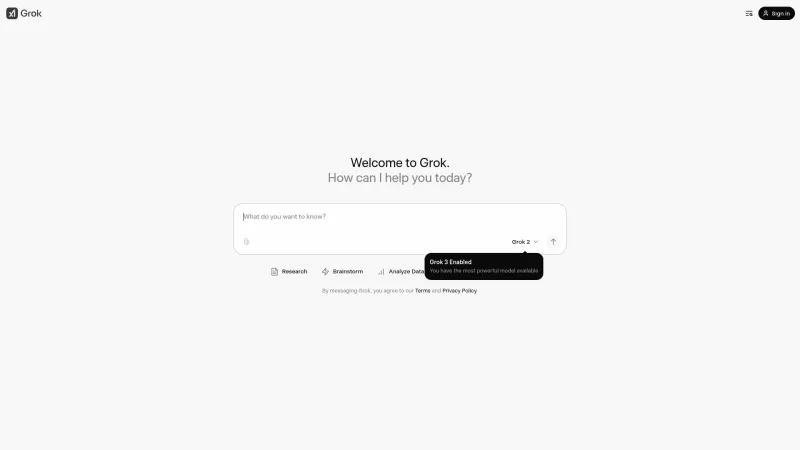
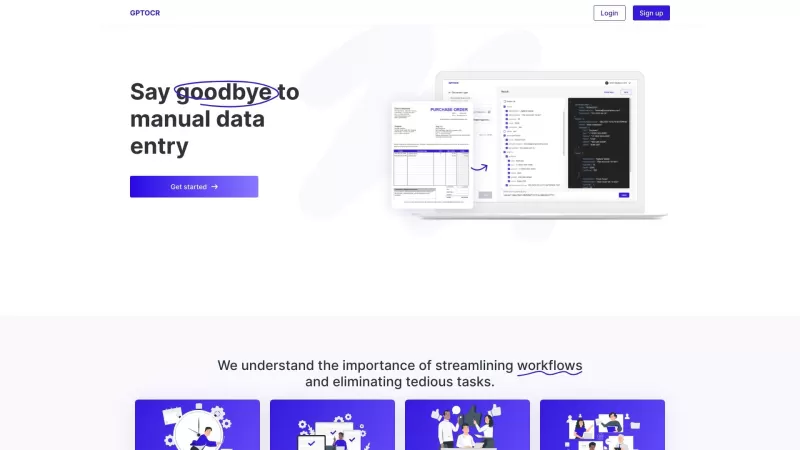
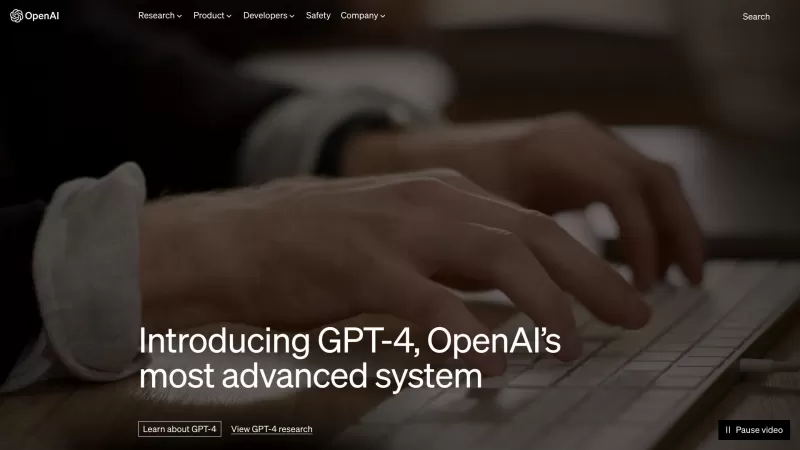
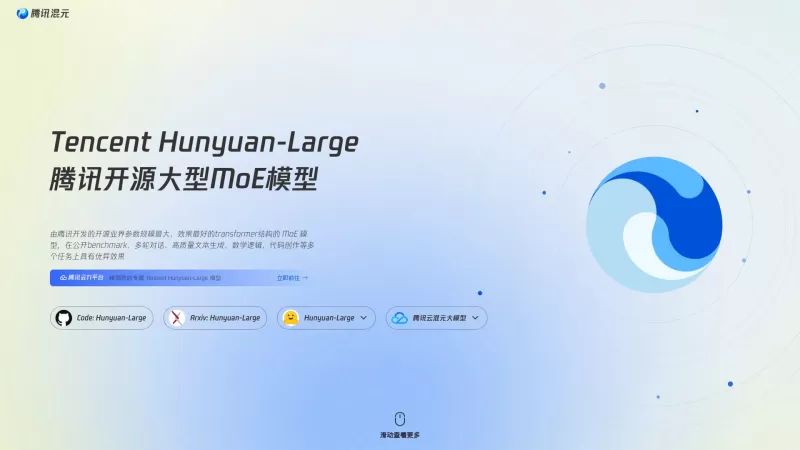
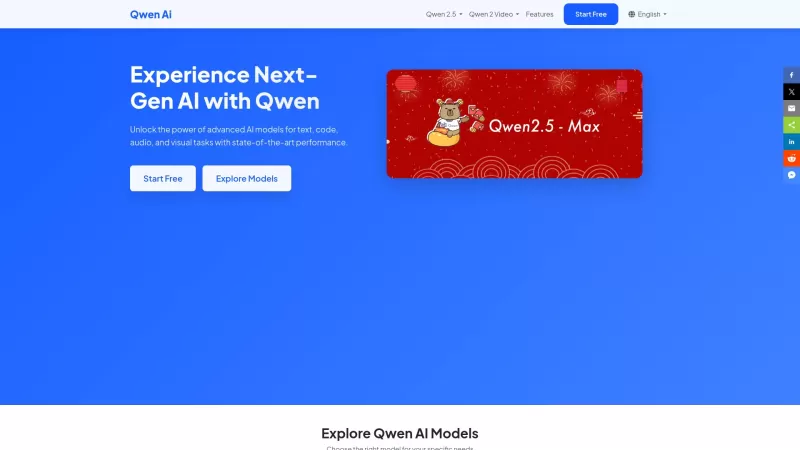
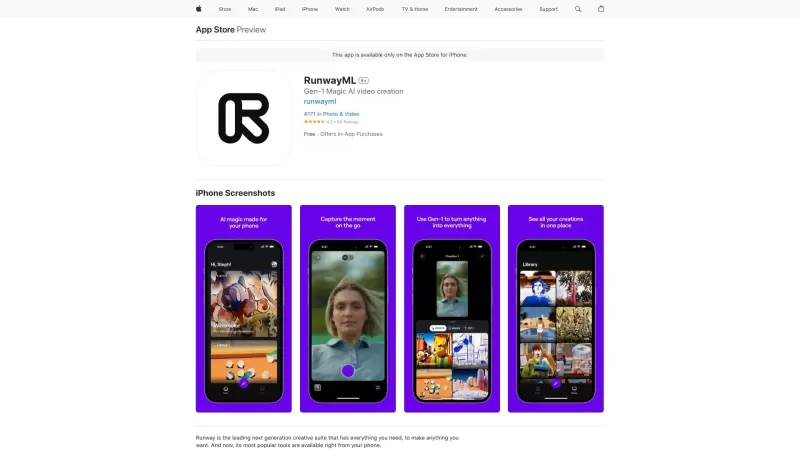